Whats A Building Envelope?
A building envelope is comprised of the components that make up the shell of the building. The components separate the exterior from the interior of the building and are designed to meet or exceed the needs of the specific application. There are many new materials and improved building codes designed to increase the life and efficiency of your home. The building envelope must be designed with regard to climate, ventilation, and energy consumption within the building. The improper install of the components that make up the buildings envelop can cause costly damage and energy loss.
Insulation

Expanded polystyrene (EPS)
The most versatile of the three rigid insulation options, EPS is used in Roof, Wall, Floor, Below Grade & Structural GeoFoam applications. EPS foam is the insulation used most widely in insulated concrete forms and structural insulated panels. With the highest average R-value per dollar of the three types of rigid-foam insulation (about 4.6 R per inch), EPS foam costs the least, while meeting or exceeding all required building and energy codes. EPS is approved for ground contact, below grade applications and can be treated to resist insects, and it does not retain water over the long term. When applied as sheathing, EPS should be used over house wrap, or with a product that incorporates a factory laminated option. EPS is available faced or unfaced. Faced products are considered vapor retardant and specialty products are considered vapor barriers. EPS manufacturers (such as Insulfoam) typically warrant 100% of EPS’ R-value over the long term as EPS foam R-value does not degrade over time.

Extruded polystyrene (XPS)
Easily recognized by its blue, green, or pink color, extruded polystyrene falls in the middle of the three types of rigid-foam insulation in both cost and R-value. Used most in walls or below grade applications, XPS is recyclable, and at about R-5 per inch, costs around 42¢ per sq. ft. for a 1-in.-thick 4×8 panel. XPS comes unfaced or with a number of different plastic facings. Unfaced 1-in.-thick XPS has a perm rating around 1, making it semipermeable. Thicker and faced XPS is stronger and can have a lower perm rating, but either way, it is considered a vapor retarder, not a vapor barrier. XPS absorbs more moisture than other insulations over the long term, and as a result, its warranty doesn’t honor R-value retention over the long haul.

Polyisocyanurate (Polyiso, ISO)
Most used in roofing applications, ISO panels are expensive, costing as much as 70¢ per sq. ft. for a 1-in.-thick panel, and they pay off with (aged) R-values as high as R-6.5 per inch. (R-values start around R-8 and degrade slightly over time.) The manufacturing process for ISO is one that is not environmentally friendly, and starts with liquid foam, further ISO is not able to be recycled. Because ISO starts as liquid foam and has to be sprayed against a substrate to form a rigid panel, all ISO panels are faced. A few different facings used on ISO affect the performance of the panel in both durability and perm rating. Foil-faced ISO panels are considered impermeable. Because applying these products as sheathing creates an exterior vapor barrier, they never should be used with an interior vapor barrier. More permeable ISO panels are faced with fiberglass and can be used without creating a vapor barrier.

Halo Interra, Exterra, & Subterra
Zero thermal drift. Zero compromise
-
GPS (graphite polystyrene) provides R-5 per nominal inch*
-
GPS provides a permanent long-term R-value and won’t deteriorate over time like XPS and ISO.
-
GPS delivers greater R-values at lower outside temperatures.
-
Minimizes the energy loss from thermal bridging
-
Light yet durable — perfect for today’s demanding jobsites.
-
Superior indoor air quality due to Greenguard certified Neopor® GPS core.
-
GPS is 100% recyclable and ozone layer-friendly — no CFCs or HCFCs.
-
Breathable
Siding
FIBER CEMENT SIDING
PROS
-
Longevity: Most hardie board siding comes with a 50-year, limited transferable warranty. This siding is completely rot and insect resistant and can even handle salt spray from the ocean.
-
Appearance: Hardie board siding can be made to mimic just about any other siding material, including wood lap boards, cedar shingles, and wood shake siding. Color options are virtually unlimited. These colors are accompanied by a 15 year warranty on the finish.
-
Fire Resistance: Hardie board siding is 90 percent sand and cement which makes it fire-resistant. Case in point, a St. Paul Minnesota house fire torched two fire trucks parked 60 feet away, but the cement board siding home next door, 50 feet away, remained unscathed.
-
Storm Resistance: Whether you’re looking for a siding material that can withstand the next Katrina, or one that can fend off the next summer hailstorm without sustaining damage, cement board siding is a proven commodity in the weather department.
CONS
-
What’s not to like about hardie board siding? Two things stand out. First of all, because of its weight, the siding requires more resources to install than other siding materials. Second, it’s not a maintenance-free siding material. You will have to repaint it in time.
-
High Installation and Labor Costs: Hardie board siding requires more planning, a larger labor force, and takes longer to install due to its composition. It weighs about 300 pounds (100 square feet) compared to 60-70 pounds for vinyl siding. This can increase labor and the cost of cement installation.
-
Maintenance: It has to be re-painted periodically. Hardie board’s ColorPlus ® Technology Warranty covers paint and labor for peeling and chipping of their finishes for only 15 years.
-
Re-caulking of seems and trim.
-
Hard to repair if broken. ​
VINYL SIDING
PROS
​
-
The question still stands: how long does vinyl siding last? The simple answer is a long time, but the exact time frame is tough to pin-point. With absolutely no effort or cleaning, your vinyl siding will still last you about 60 years.
-
That being said, if you properly clean your vinyl siding and keep it maintained, it’ll last you much longer. How much longer you ask? Upwards of 100 years! You won’t get that with other siding materials which is why vinyl is the perfect option for homeowners.
-
Low to no maintenance. Vinyl siding should be occasionally cleaned to remove mold or mildew before it stains the PVC. This is done with a nylon brush and a 3:7 vinegar and water mix. Avoid using your power washer, however - it will force water up behind the siding and can cause mold problems inside your home. Re-painting and re-sealing is in the past.
-
Variety of colors and styles. We're talking way beyond just clapboard here. Vinyl siding comes in a wide variety of styles, including shingles/shakes, dutch lap, vintage scallops and is available in range of colors to suit any existing woodworking or painted accents on your building.
-
Earth friendly. If you're considering going for a LEED certification for your home or business, you can investigate vinyl siding options manufactured using recycled material, which not only keeps the plastic out of the landfill now, it keeps it out when it reaches the end of its usable lifespan and is recycled again.
-
Over 60 years' of improvements. Vinyl siding has been on the market since the 1950's. Though it's had a bad rap because of initial quality problems, those issues have been solved and the technology improved upon to include color and material stabilizers, UV protection and many other advancements over the years.
CONS
​​
-
Sagging in thin siding. In lower-quality, thinner siding, you may experience sagging between nails, especially as the siding ages in the heat.
-
Wind problems. As another thin-siding issue, it's a great example of you get what you pay for. Better-quality, heavier vinyl siding is often rated to hurricane-force winds.
-
Expansion and contraction. Don't like the look of all the trim at the corners and every junction? Don't go with vinyl. The trim is needed to give it room to expand and contract with the temperature.
-
Fading. Though you won't see as much as in previous decades, there can be a noticeable difference when you're making a repair and splicing in a new piece of siding.
VS



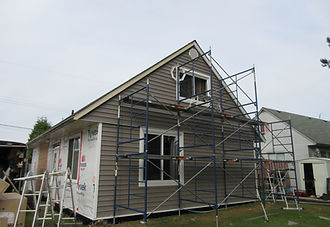



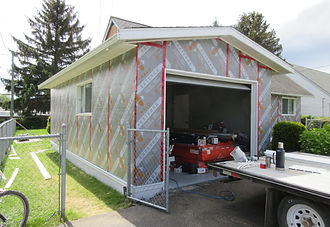
we are only a phone call away